Nail clippers: a seemingly simple tool, yet their creation is a fascinating journey through precision engineering and manufacturing prowess. This ubiquitous household item, invented over a century ago, has undergone continuous refinement, evolving from a revolutionary alternative to scissors to the highly engineered product we know today. From its humble beginnings as a convenient and affordable solution, the nail clipper has become a global staple, found in billions of homes worldwide. This article delves into the intricate process behind their manufacture, revealing the surprising complexity hidden within this seemingly uncomplicated object.We will explore the transformation of raw steel sheets into the finely crafted components of a nail clipper, highlighting the sophisticated machinery and skilled labor involved. From the initial shaping with a meter-long die to the meticulous final polishing and sharpening, we will uncover the various steps that contribute to the creation of this everyday tool. Discover the hidden intricacies of assembly, the precision drilling and riveting that ensures smooth operation, and the meticulous quality control measures that guarantee a consistently high-quality product. Prepare to be amazed by the journey from raw material to the finished, functional nail clipper.
Pros And Cons
- Still popular over a century after its invention.
- Millions are sold.
- Essential part of many manicure sets.
Read more: Top 10 Baby Nail Clippers: Our Expert Picks
A Brief History of Nail Clippers
Invented in 1896 in the United States, nail clippers quickly gained popularity. By 1902, they were widely available, marketed as a convenient and affordable alternative to scissors. Sold by the dozen for just $2, these small tools revolutionized personal grooming.
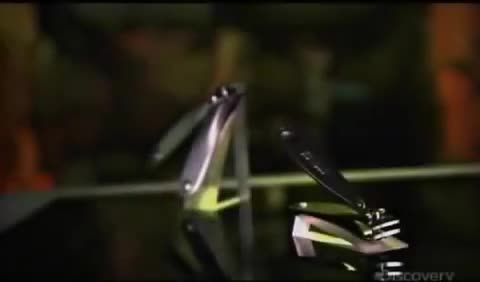
Their ingenious design provided a simple yet effective solution for nail trimming, unlike the cumbersome process of using scissors. This simple device became a staple in households worldwide, a testament to its practicality and enduring appeal.
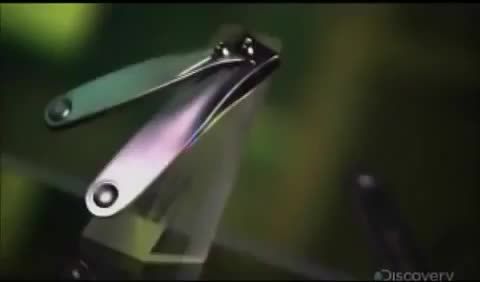
The Manufacturing Process: From Steel Sheet to Finished Product
The journey of a nail clipper begins with a long, intricate die. This meter-long tool shapes the steel sheets into the initial forms of the clipper components. Hydraulic machinery forces the steel sheets through the die's various openings, creating the jaws, levers, and other parts.
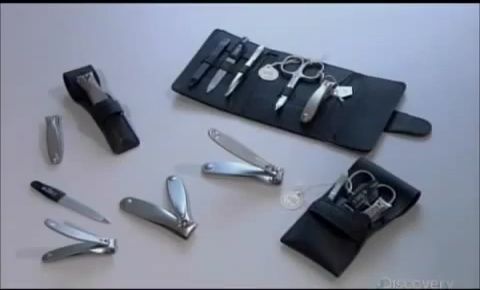
The process involves multiple steps and shaping techniques to turn a flat sheet of steel into the complex shapes required. It's fascinating to observe the transformation of raw material into recognizable parts. After 80 strokes in just one minute, a dozen nail clippers are born.
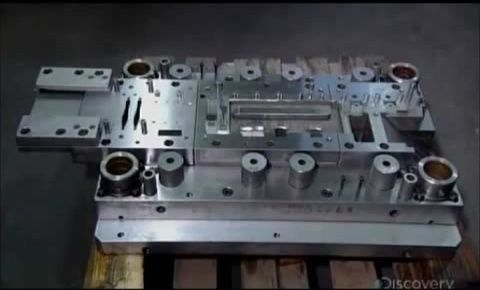
The jaws are further refined by a vibratory process using abrasive stones and organic acids. This polishing ensures a smooth, gleaming finish without compromising the sharpness of the cutting edges.
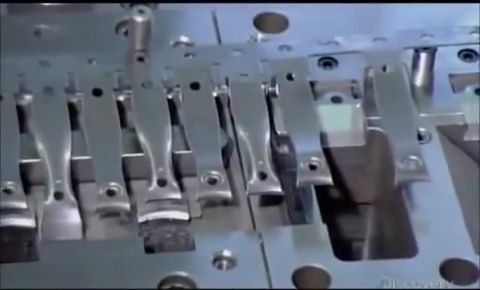
Assembly and Finishing Touches
Assembly begins with aligning the clipper jaws and riveting them together. A mechanical press secures the rivet, preventing the jaws from twisting apart. The gripping end is then smoothed and evened out using an abrasive wheel, creating a seamless look.
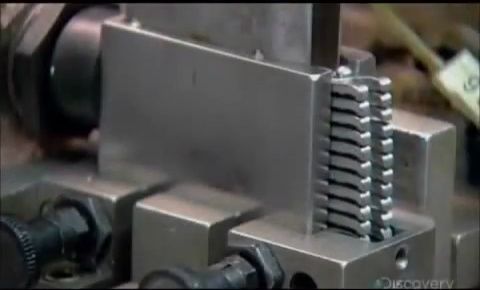
After securing the jaws, the focus shifts to the lever mechanism. Holes are precisely drilled into the lever prongs, allowing a pin to secure it to the jaws. This complex process ensures the lever's smooth and reliable movement.
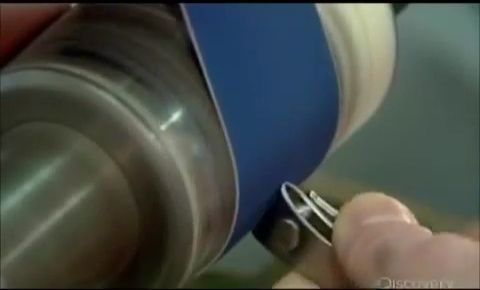
The final steps involve cleaning the clippers, etching the company name and item number, and carefully sharpening the cutting edges. This meticulous attention to detail ensures each clipper meets quality standards.
Conclusion: The Enduring Appeal of a Simple Tool
The manufacturing process of nail clippers is a testament to the precision and efficiency of modern manufacturing. While seemingly simple, the creation of these tools involves a complex series of steps, requiring skilled labor and advanced machinery.
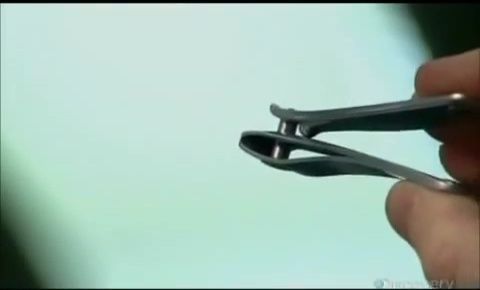
From a simple invention to a globally used tool, nail clippers continue to provide a convenient solution for nail care. The detailed process shows how much effort goes into creating an item people take for granted. It's a compelling illustration of how everyday objects are manufactured.
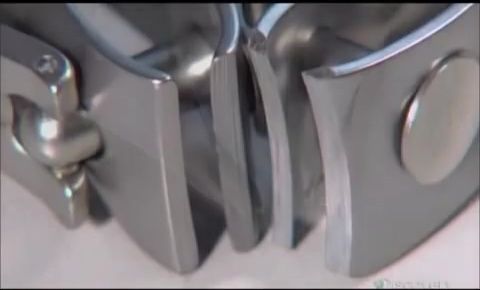